The factory of the future: Unlocking Industry 5.0 for manufacturing resilience
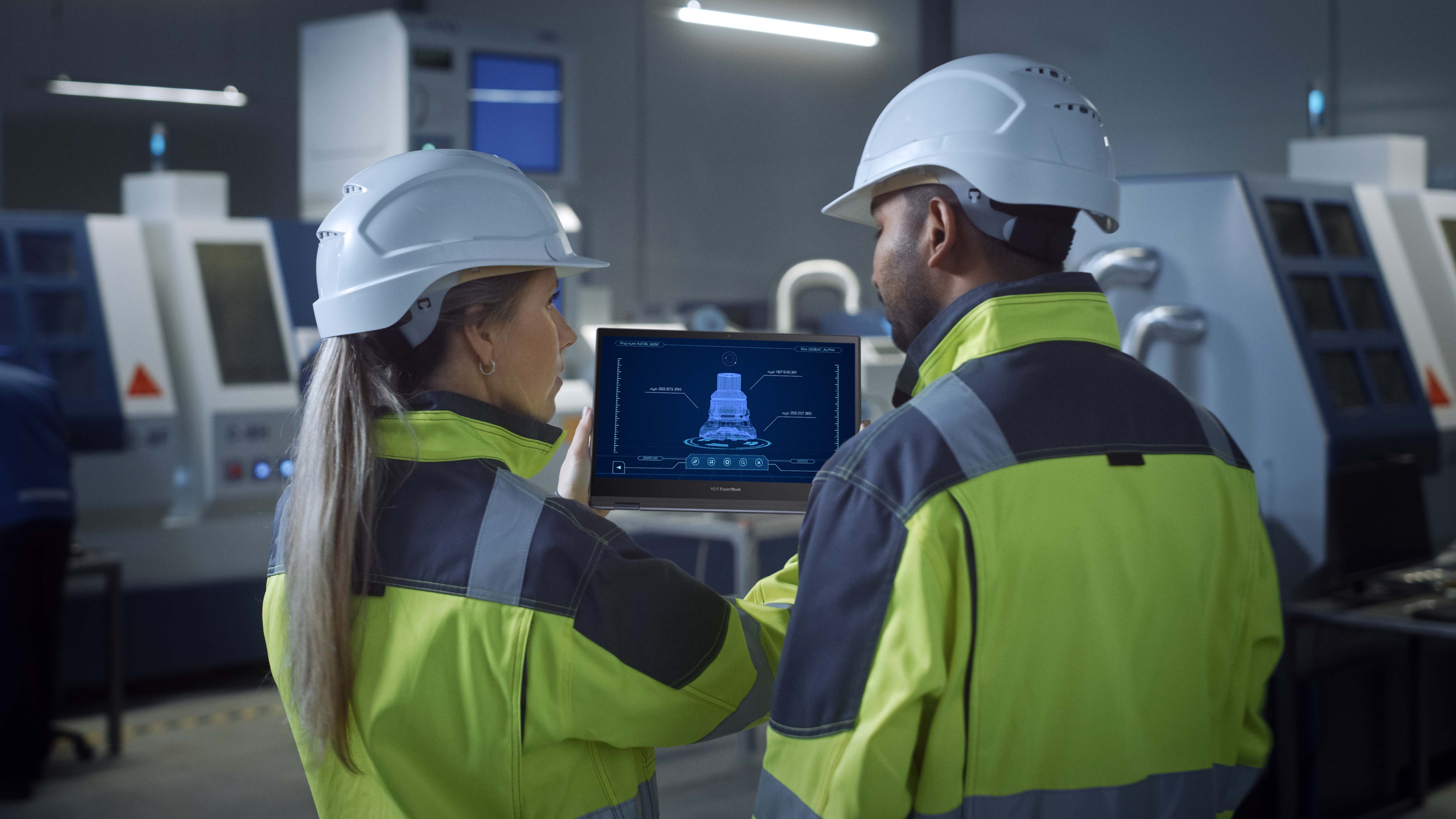
Like almost every other industry, manufacturing has been hit hard by the global COVID-19 pandemic. According to Kearney1, more than 75% of the world’s global manufacturing output has been directly impacted by the crisis. As the world faced rising cases, lockdowns, travel restrictions and more, manufacturers have had to grapple with unprecedented disruptions to production lines and supply chains.
87% of executives now acknowledge the need to overhaul manufacturing and supply networks to increase future resilience2. In another survey by Gartner3, more than half expect to be highly resilient within two to three years. As risk competitiveness and business continuity take priority, leaders in the field are increasingly seeing that advanced digital technologies are indispensable.
Pertinent lessons from COVID-19
Manufacturers face challenges that are varied and complex. The fallout from the pandemic has made it clear that supply chains are too long and complex, often depending on a single source of supply. Manufacturers now seek to reduce complexity and to enhance the agility of their supply chains. They need to be able to move supply, production, and distribution activities around more flexibly to adapt to changing circumstances.
As manufacturing companies shift back to work in the new normal, social distancing measures and employee safety will continue to remain important. Under such conditions, Gartner estimates that up to half of workers will still be unable to do their jobs onsite4. In the post-pandemic era, manufacturing offices and factories need to be able to support remote working or even ‘lights out’ – meaning fully automated – manufacturing to keep up a competitive pace of production.
But the greatest risk lies in the unknown. Future pandemics, natural disasters, cyber-attacks and more could significantly alter consumer behaviour, supplies and manufacturing processes once again. During COVID-19, the most resilient companies were able to pivot on a dime – altering product lines to manufacture Personal Protective Equipment (PPE), face masks and other essentials to stay relevant. While not every factory can or needs to change product lines so drastically, manufacturers should aim to achieve the agility that will serve them well in future crises.
Digital priorities for resilient factories and supply chains
Of course, it’s not about implementing digital technologies for the sake of it. Industry 5.0, building on Industry 4.0, requires manufacturers to place humans at the heart of everything – so that man and machine work seamlessly to allow for high levels of precision and efficiency alongside a special human touch. The European Commission has recognised Industry 5.0 as integral to resilient industries and societies, as it supports and empowers innovation, workers and environments5.
Cloud service to support agile operations
Agile operations start with end-to-end, real-time visibility across the organisation. Leaders need a holistic view of the business from the office and factory floor, machines and mobile devices, and across the connected network of suppliers and distributors. Comprehensive cloud services and complete edge devices help to connect data across the organisation, giving leaders real-time knowledge of supply and demand fluctuations, availability of labour, machine maintenance and more. This sort of information is the crucial foundation for manufacturing agility and flexibility.
Digital intelligence to enhance decision-making
The next step is to embed data analytics and intelligence into manufacturing processes. Artificial intelligence (AI) can also drive the predictive analysis of thousands of logged events to search for abnormal signals in single assets. AI-powered automated optical inspection can spot defects more quickly and accurately than manual inspection is able to. The use of AI, ML and automation has many applications across the manufacturing organisation, driving quick and informed decisions that enhance operations and save time, money and resources.
Powerful devices to empower the workforce
EY noted that 77% of executives in Europe plan to transition to lean or additive manufacturing such as 3D printing to “gain advantages in speed, cost, precision and materials”6. Manufacturers must prepare themselves for this future reality by investing in the right talent and training, as well as by equipping employees with the appropriate digital tools. Laptops and desktops must be powerful enough to handle 3D design and printing, alongside virtual reality (VR) and augmented reality (AR) technologies that will feature more heavily as Industry 5.0 comes to maturity. Immediate benefits include support for a remote-working and decentralised workforce, ensuring resiliency even in times when onsite work many not be possible.
Adapting for the future is a necessary pain
Moving towards Industry 5.0 will not be easy, but the consequences of inaction are far harder to bear. COVID-19 has exposed vulnerabilities in manufacturing lines and supply chains, offering a unique opportunity for organisations to get the ball rolling on truly transformational change. Manufacturers need to seize the moment, embrace advanced digital technologies, and start building resilient businesses of the future.
Related Article
1 Kearney, Building resilience in manufacturing and supply chains
2 Gartner, Survey finds 87% of supply chain professional plan to invest in resilience
3 Gartner, 6 strategies for a more resilient supply chain
4 Gartner via Orange Business Services, How manufacturers can become more resilient
5 European Commission, Industry 5.0: Towards more sustainable, resilient and human-centric industry